Every Day Is Earth Day in This Mason Gross Class on Upcycling

Costume Director Denise Wagner’s class on fast fashion helps students understand the work that goes into making their clothes
The room known as the costume shop is usually reserved for Mason Gross classes, where students design and construct many of the garments worn in Rutgers Theater Company productions. But on Tuesday afternoons, the space is transformed for a class open to all university students that seeks to make a difference by delving into the modern textile industry.
For two years now, Costume Director Denise Wagner has taught students majoring in everything from dance to marine biology sustainable tips and tricks in “Upcycling: An Artistic Response to the Environmental Effects of Fast Fashion.”
“There’s a big problem with fast fashion,” Wagner says, referring to the rapid speed at which many clothing brands produce and advertise their merchandise. “I wanted to delve deeper into that and start putting solutions out there, making change.”
With 92 million tons of textile waste being produced every year, Wagner says the goal of the class is for students to gain a broader understanding of where their clothes come from, what they’re made of, and who does the work of creating them.

Throughout the semester, students read and discuss Maxine Bédat’s Unraveled: The Life and Death of a Garment, which follows a pair of jeans from the beginning of its “life” to the end, tracking the global supply chain behind mass-produced clothing. The novel touches on the environmental impacts of cotton farming, the humanitarian concerns around dyeing, weaving, and sewing factories, and the dilemma of what to do with the sheer amount of clothing that’s donated or thrown away every day.
Emma Giovenco, a third-year student studying Information Technology and Informatics, already knew about the issues involved with fast fashion. She’s a member of R U Thrifty, a club on campus dedicated to sustainable fashion education, but still found herself impacted by Unraveled and the documentaries they watched in class.
“It’s hard to see the conditions people doing the sewing are under, and learning how low the wages are,” she says. “It really affected me.”
As the students learn more about the reality of fast fashion, Wagner weaves in hands-on activities that teach fundamental skills for embellishment and repair, providing them with strategies for extending the life of a garment.
“The more we use what we already have, the more it stays out of a landfill,” Wagner says. “The less we buy, the less ends up there.”
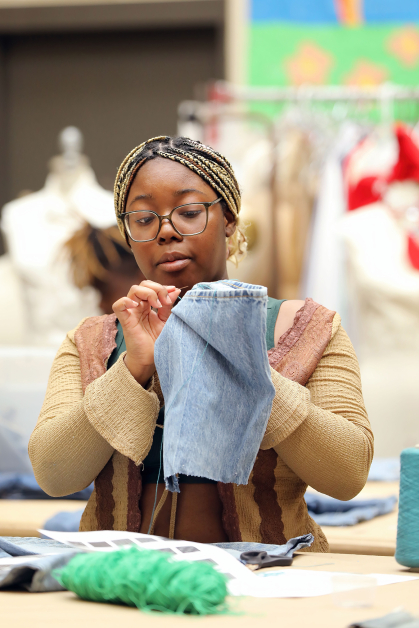
When it came to deciding which activities to include in the syllabus, Wagner says she drew from techniques from before the fast fashion boom. Students learn to fix tears and patch holes using Sashiko, a Japanese technique for visible mending, and even weave their own 1940’s “Make Do and Mend” pins using scrap wire from the university’s OIT department.
For their lesson on tie-dye, Wagner sourced materials from around the workshop and the university. Wagner collected discarded white shirts from the theater company for the canvases, and worked with students to create natural dyes using marigolds from her garden, onion scraps from nearby Harvest Cafe, and local produce like cranberries and purple cabbage. Even rusty odds and ends from the scene shop next door created a muted wash when soaked in water and vinegar. (And, of course, handled with gloves.) The once-abandoned fabric was transformed into colorful shirts, bandanas, and scarves.
“The way that fashion has changed, it’s become disposable,” says Jennifer Duarte, a first year studying marine biology. “People used to hang onto their clothes for a long time. The shrinking quality of stuff is even more reason to make your own thing, or to repurpose something you already have.”
Outside of class, Wagner and the rest of the costume area are working to reduce their own textile waste. Nearly every garment created by costume students is kept in the second room of the Costume Shop, and many are reworn for other performances or taken apart and remade into something new. Assistant Costume Director and costume design alum Brian Mulligan even recalls flipping a 17th century gown into a 1960’s-inspired ensemble. Wagner has also partnered with Helpsy, a clothing collection company, to recycle fabric scraps after projects have been completed, and is working on introducing Helpsy’s collection bins to campus in the future.