Recycled Plastic Lumber Invented by Pioneering Rutgers Professor
Thomas Nosker created the synthetic lumber – made from recycled plastic bottles, coffee cups and other plastics – used in bridges, railway ties, docks and picnic tables
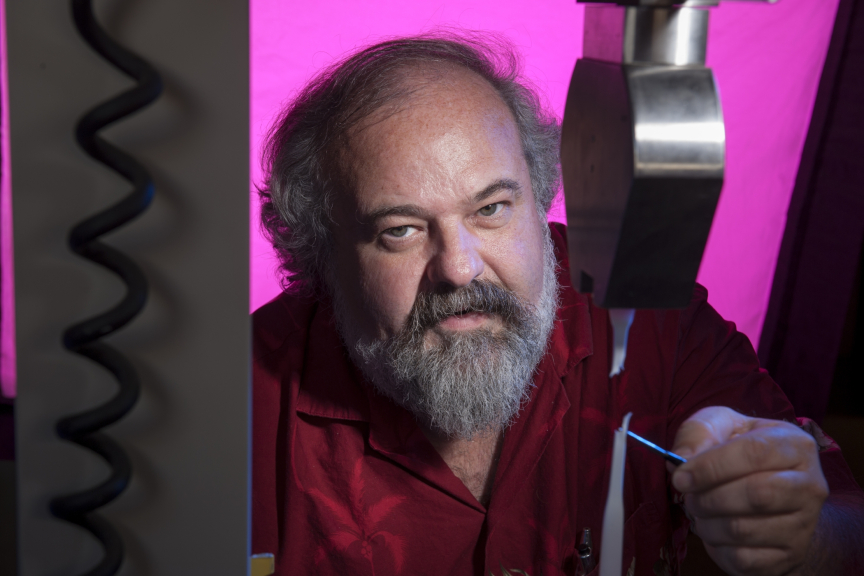
'People complain about plastics because they don’t degrade. We found a way to turn that to our advantage with a product.'– Thomas Nosker
Imagine a material lighter than steel, longer lasting than lumber, and strong enough to support 120-ton locomotives.
Now imagine that material is made from milk containers, coffee cups, and other plastics that we recycle.
It’s called structural plastic lumber, and the ingenious, nontoxic material was invented by Thomas Nosker, a professor in the Rutgers University–New Brunswick Department of Materials Science and Engineering and Center for Advanced Materials via Immiscible Composite Materials. The late Richard W. Renfree, Nosker’s graduate student who later became a Rutgers professor, helped invent the revolutionary material.
“People complain about plastics because they don’t degrade,” Nosker says. “We found a way to turn that to our advantage with a product.”
That product is increasingly used to build bridges on U.S. Army bases and for other items—docks, picnic tables, park benches, and other structures across America and overseas. It’s been used to make about 1.5 million railway ties in the United States alone. Since each tie weighs about 200 pounds, that means roughly 300 million pounds of plastics have not ended up in landfills, won’t choke marine life, and won’t soil beaches.
Nosker, a prolific inventor, and his colleagues have been on the leading edge of plastics research for decades. They developed several types of structural recycled plastic lumber, a standard way to test plastic lumber, fire retardants for plastic lumber, and machines to make plastic lumber. All told, Nosker co-holds 28 patents or patents pending in the United States, in addition to overseas patents, reaping millions of dollars in revenues for Rutgers.
Thirty years ago, Nosker was a doctoral student at Rutgers trying to deal with growing mountains of discarded containers. Plastics were rapidly replacing glass for packaging milk and soda, two high-volume grocery products, and ending up in landfills.
Nosker and others devised ways to sort, clean, and process soda bottles made from polyethylene terephthalate (PET). They sold the material for a profit to make rugs and insulated jackets, to stuff mattresses, and even to produce new soda bottles. Far more problematic was another type of plastic waste, known as high-density polyethylene (HDPE), that was used to make milk containers.
“Prices for HDPE were so low that you couldn’t even afford to wash used milk bottles in preparation for recycling,” Nosker says. “But we couldn’t just turn around and throw it away. Plastics experts said it was potentially recyclable, and we wanted to work on that.”
Initially, Nosker and his colleagues tried making bottles into a substitute for chemically treated wood used in park benches and decks. But recycled HDPE planks sagged over time, when people repeatedly sat or walked on them. Some researchers tried combining HDPE with other plastics used to package foods and household goods, but had little success.
Then Nosker found a workable formula.
“We combined HDPE with polystyrene from old Big Mac containers,” Nosker says. At a specific proportion, the blended plastics gained strength because of the way the tiny plastic particles interlocked.
Making the leap from creating strong recycled plastics to using them to build objects traditionally made of wood required an innovative show-don’t-tell strategy. For centuries, wood lumber from trees has been the go-to durable, flexible, and affordable raw material for construction. But wood has its drawbacks; it needs protection from insects, other animals, and the elements, and it is often treated with toxic preservatives that can leach into soil, water, and groundwater—posing risks to people, animals, and plants. Structural recycled plastic lumber, which is mostly polyethylene reinforced with stiffer plastics or recycled composites like car bumpers, does not pose such risks.
So 18 years ago, Nosker and Richard G. Lampo, a materials engineer at the Construction Engineering Research Laboratory of the U.S. Army Corps of Engineers in Champaign, Illinois, built the first structural recycled plastic lumber bridge for vehicles at Fort Leonard Wood in Missouri.
“The industry was making a lot of picnic tables and park benches and those are good applications, but we were trying to push the envelope with our applications and do it cost effectively,” says Lampo, who recently visited the Fort Leonard Wood bridge. “It is holding up fine.”
Today, Nosker’s invention is gaining popularity in environmentally sensitive areas where railroads cross streams and where plastic tie durability is a plus. The Chicago Transit Authority, for example, found the plastic ties an economical choice for track rehabilitation on its elevated lines.
Nosker helped build New Jersey’s first structural recycled plastic bridge in 2002, in the environmentally fragile Pine Barrens. The bridge, with its revolutionary I-beam design, has weathered the elements well and continues to carry cars.
More recently, two active, rural Army bases wanted bridges for hefty loads. In Fort Bragg, North Carolina, where the Army has tank training grounds, bridges must carry heavy vehicles across numerous streams throughout the 160,000-acre base. The Army successfully demonstrated the first structural recycled plastic bridge to support a 73-ton M1 Abrams tank there in 2009, and has ordered 1,000 more plastic bridges for Fort Bragg and other sites.
Structural plastic lumber bridges also have been built at Fort Eustis in Virginia, as well as in civilian areas of California, Maine, Ohio, Scotland, and other locales.
Rutgers has licensed its award-winning plastic technology to two companies that make railroad ties and building products from recycled materials: AXION International Inc. of Zanesville, Ohio; and London-based Sicut Enterprises Limited.
Nosker is proud of his role in trailblazing plastics research. “I’m grateful that I’ve been able to have such a fun career,” he adds.
And the best may be yet to come.
His team is developing light but super-strong graphene-plastic materials that could be used in next-generation tanks, personnel carriers, Humvees, and civilian vehicles and products such as bicycles. Graphene comes from the graphite commonly used in pencils.
“I think the graphene stuff is going to eclipse the work in recycling,” Nosker says. “I might not be around to see people recognize that universally, but I think it’s a big discovery.”
Read about more Rutgers Revolutionaries
For more information, please contact science communicator Todd B. Bates at tbates@ucm.rutgers.edu or 848-932-0550.